Machine introduction
W10 plate rolling machine is a fully automatic hydraulic stainless steel plate rolling machine. This machine is widely used in the metal processing industry for its high efficiency, stability and precise operation performance, especially in the rolling process of stainless steel materials.
Working Principle
Placing the sheet metal: The operator first ensures that the sheet metal is placed between the bottom rollers of the coiler and that it is level and properly aligned. This step is very important because any error in the initial positioning can lead to incorrect dimensions of the final product.
Adjust the upper roller and apply pressure: Once the sheet is positioned, the top roller is lowered hydraulically or mechanically to apply pressure to the sheet. The descent speed and pressure of the top roller can be adjusted according to the thickness of the sheet and the characteristics of the material, thus achieving the desired bending effect without damaging the material.
Pre-bending of the edges to create the initial curvature: The pressure of the upper roll first bends the edges of the sheet to create the first curvature. This process underpins the entire rolling process and determines the shape and direction of the subsequent rolls.
Multiple roll adjustments: The sheet is rolled and adjusted several times between the rolls to achieve the final shape and diameter. After each roll, the operator checks the shape of the sheet and, if necessary, makes fine adjustments to ensure that the rolled part meets the specifications on the design drawing.

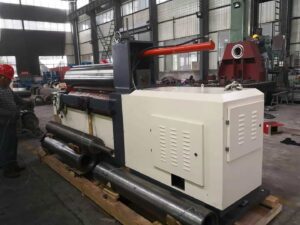
Features of W10 Plate Rolling Machine
Fully Automatic Hydraulic System: The W10 plate rolling machine utilizes an advanced fully automatic hydraulic system to ensure ease of operation and processing accuracy.
Specialized for Stainless Steel Materials: Designed for stainless steel materials, it is capable of processing stainless steel plates of various thicknesses and widths.
High Efficiency: The high efficiency design of the machine allows for a significant increase in production speed and a reduction in processing time.
Easy Maintenance: The design takes into account the ease of maintenance and reduces downtime.
Advantages of W10 Plate Rolling Machine
- Increased productivity The efficient operation of the W10 plate rolling machine contributes to increased production and reduced unit costs.
- Guarantees processing quality The precision rolling process guarantees the quality of the finished product and reduces scrap rates.
- Safe operation Fully automated hydraulic systems reduce direct contact between the operator and the machine, increasing operational safety.
- Reduced maintenance costs The easy-to-maintain design reduces maintenance costs and time.
Application Scenarios
- Shipbuilding: used in the production of hulls and decks to ensure the quality and safety of components.
- Architecture: For rounding roofs and walls to improve the aesthetics and usability of buildings.
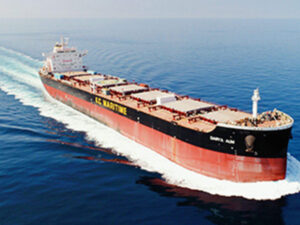
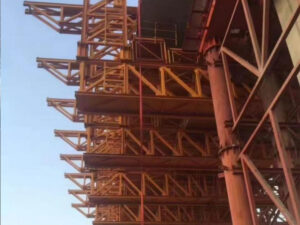
- Automotive: to produce exhaust systems, fuel tanks, etc. to ensure the precision and quality of components.
- Aviation: To produce curved parts for airplanes and spacecraft that require lightweight, pressure-resistant materials.
- Solar cells: manufacturing solar energy equipment that requires high efficiency and durability.
- Oil and gas: manufacture pipes and vessels resistant to high pressure.


Operating instructions
Prepare the material: make sure that the size and thickness of the stainless steel plate meets the requirements of the machine.
Setting parameters: Set the machine’s pressure, speed and other parameters according to the material’s characteristics and processing needs.
Start the machine: Start the machine according to the operation manual to begin the rolling process.
Monitor the process: Monitor the machine’s operating status during the coiling process to ensure the quality of the process.