Machine Introduction
The QC12Y series hydraulic swing shearing machine is a common and efficient metal processing equipment that is widely used in various metal cutting and plate processing fields. This series of shears uses an advanced hydraulic system to drive blade movement to achieve precise cutting of metal materials. It has the characteristics of multi-functional application, automated operation, energy saving and environmental protection, and provides efficient and precise cutting solutions for metal processing companies.
The QC12Y series hydraulic swing shearing machine adopts an advanced CNC system to accurately control the motion trajectory of the shearing knife to achieve cutting and cutting of the workpiece. Its hydraulic system controls shear force and cutting speed, ensuring accuracy and stability during the cutting process. The advantage of using a hydraulic system is that it can handle various complex processing requirements and can complete shearing operations quickly and accurately.


working principle of Hydraulic Swing Shearing Machine
1. Hydraulic system: The QC12Y series hydraulic swing shearing machine uses a hydraulic system to provide power. The hydraulic system consists of oil pump, oil tank, hydraulic cylinder, control valve, etc. When the work starts, the oil pump draws the hydraulic oil from the tank and transports it through the pipeline to the hydraulic cylinder, generating high pressure.
2. Pressing material: The metal sheet is placed on the workbench of the shearing machine, and the hydraulic cylinder is pressed down by pressure, so that the upper blade and the lower knife seat clamp the metal sheet and fix the position to be cut. This step ensures the stability and precision of the sheet metal during cutting.
3. Cutting: The control valve in the hydraulic system controls the hydraulic oil to enter the main cylinder to push the blade down rapidly. The upper blade and the lower blade base form a cutting action to achieve cutting of metal plates. During the cutting process, the hydraulic system provides sufficient pressure and power to ensure cutting accuracy and efficiency.
4. Return: After cutting, the hydraulic oil returns to the oil storage tank, and the blade returns to the initial position, ready for the next cutting. The control valve of the hydraulic system adjusts the flow direction and pressure of the hydraulic oil in a timely manner to ensure the smooth return of the blade and maintain the stability and continuous working ability of the equipment.

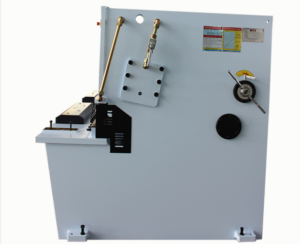
Features of Hydraulic Swing Shearing Machine
High efficiency and energy saving: The electro-hydraulic proportional adjustment system can realize quantitative oil supply and minimize energy consumption while ensuring cutting quality. Efficient hydraulic system, it uses a hydraulic system to drive blade movement, providing strong cutting force and ensuring fast and accurate cutting.
Precision CNC control and high cutting accuracy: Equipped with a CNC system to control the motion trajectory of the shearing knife to achieve high-precision cutting operations. The cutting accuracy can reach less than 0.1 mm, which can meet various precision requirements and reduce material waste. The stable pressure provided by the hydraulic system ensures precision and smooth cutting edges during cutting.
Simple operation: It adopts electrical, hydraulic and mechanical integration technology, which is easy to operate, reduces the labor intensity of the operator and improves work efficiency. The equipment is designed with safety protection devices to ensure the safety of operators. Suitable for metal plates of various materials, such as steel plates, aluminum plates, stainless steel, etc., to meet different cutting needs.
Long service life: The main components are made of high-quality materials, finely processed, and have a long service life, ensuring long-term stable operation of the equipment.Energy saving and environmental protection. Compared with traditional mechanical cutting equipment, it consumes less energy, has less noise and vibration, and meets the energy saving and environmental protection requirements of modern manufacturing.
Technical Parameters
- Models: Including 4×2000, 4×2500, 4×3200 and other models, covering plate processing needs of different sizes and thicknesses.
- Maximum cutting thickness: From 4mm to 25mm, varying according to different models.
- Maximum cutting width: From 2000mm to 4000mm, suitable for cutting plates of different widths.
- Distance between uprights: From 2150mm to 4720mm, providing sufficient shearing space.
- Working table height: 740mm to 1000mm, convenient for operation and material loading and unloading.
- Strokes: The number of strokes per minute varies depending on the model.
- Back gauge stroke: 20-1000mm, adjustable, suitable for sheet cutting of different lengths.
- Shearing angle: It varies depending on the model.
- Throat depth: 100mm to 200mm, providing sufficient depth to meet the cutting needs of different materials.
- Main power supply: Power ranges from 4kw to 45kw, varying according to different models and work requirements.
- Overall dimensions: From 2500×1600×1550mm to 4850×2500×2350mm, adapting to the installation needs of different sites.
Model | Max.Shearing Thickness | Max.Shearing Width | Distance Between Uprights | Working Table Height | Strokes | Back Gauge Stroke | Shearing Angle | Throat Depth | Main Power | Dimensions | |
mm | mm | mm | mm | Min-1 | mm | ° | mm | kw | mm(L×W×H) | ||
4×2000 | 4 | 2000 | 2150 | 740 | 20 | 20-550 | 1°30′ | 100 | 4 | 2500×1600×1550 | |
4×2500 | 4 | 2500 | 2700 | 740 | 18 | 20-550 | 1°30′ | 100 | 4 | 3100×1600×1550 | |
4×3200 | 4 | 3200 | 3410 | 800 | 14 | 20-550 | 1°30′ | 150 | 4 | 3800×1700×1650 | |
4×4000 | 4 | 4000 | 4220 | 800 | 10 | 20-550 | 1°30′ | 150 | 5.5 | 4650×1900×1750 | |
4×4500 | 4 | 4500 | 4720 | 800 | 8 | 20-550 | 1°30′ | 150 | 5.5 | 5150×1900×1750 | |
6×1500 | 6 | 1500 | 1660 | 780 | 20 | 20-550 | 1°30′ | 150 | 7.5 | 2000×1760×1650 | |
6×2500 | 6 | 2500 | 2720 | 780 | 17 | 20-550 | 1°30′ | 150 | 7.5 | 3100×1650×1600 | |
6×3200 | 6 | 3200 | 3420 | 800 | 14 | 20-550 | 1°30′ | 150 | 7.5 | 3800×1750×1650 | |
6×4000 | 6 | 4000 | 4220 | 800 | 10 | 20-550 | 1°30′ | 150 | 7.5 | 4650×1850×1750 | |
8×1500 | 8 | 1500 | 1660 | 800 | 20 | 20-550 | 1°30′ | 150 | 7.5 | 2000×1860×1750 | |
8×2500 | 8 | 2500 | 2720 | 800 | 14 | 20-550 | 1°30′ | 150 | 11 | 3100×1750×1700 | |
8×3200 | 8 | 3200 | 3440 | 800 | 10 | 20-550 | 1°30′ | 150 | 11 | 3800×1850×1750 | |
8×4000 | 8 | 4000 | 4230 | 800 | 8 | 20-550 | 1°30′ | 150 | 11 | 4600×1900×1800 | |
10×1500 | 8 | 1500 | 1660 | 800 | 20 | 20-550 | 1°30′ | 150 | 11 | 2100×1860×1800 | |
10×2500 | 10 | 2500 | 2720 | 800 | 12 | 20-550 | 1°30′ | 150 | 11 | 3100×1750×1700 | |
10×3200 | 10 | 3200 | 3440 | 800 | 10 | 20-550 | 1°30′ | 150 | 11 | 3800×1850×1750 | |
10×4000 | 10 | 4000 | 4230 | 800 | 8 | 20-550 | 1°30′ | 150 | 11 | 4600×1900×1800 | |
12×1500 | 12 | 1500 | 1680 | 800 | 14 | 20-550 | 2°9′ | 150 | 15 | 2200×2000×1850 | |
12×2500 | 12 | 2500 | 2760 | 810 | 10 | 20-750 | 1°50′ | 150 | 15 | 3200×2000×1850 | |
12×3200 | 12 | 3200 | 3465 | 810 | 10 | 20-750 | 1°45′ | 150 | 22 | 3850×2150×2000 | |
12×4000 | 12 | 4000 | 4265 | 810 | 7 | 20-750 | 2° | 150 | 22 | 4700×2300×2100 | |
16×1500 | 16 | 1500 | 1680 | 800 | 10 | 20-550 | 2°30′ | 150 | 22 | 2600×1950×1800 | |
16×2500 | 16 | 2500 | 2765 | 850 | 8 | 20-750 | 2°9′ | 150 | 22 | 3200×2150×2050 | |
16×3200 | 16 | 3200 | 3455 | 860 | 7 | 20-750 | 2°9′ | 150 | 22 | 4000×2300×2150 | |
16×4000 | 16 | 4000 | 4285 | 900 | 6 | 20-750 | 2°9′ | 150 | 22 | 4850×2500×2350 | |
20×2500 | 20 | 2500 | 2815 | 860 | 6 | 20-750 | 2°30′ | 150 | 30 | 3450×2350×2200 | |
20×3200 | 20 | 3200 | 3487 | 890 | 5 | 20-750 | 2°30′ | 150 | 30 | 4050×2450×2250 | |
20×4000 | 20 | 4000 | 4305 | 990 | 5 | 20-750 | 2°20′ | 150 | 30 | 4900×2300×2450 | |
25×2500 | 25 | 2500 | 2805 | 900 | 5 | 20-750 | 3°7′ | 150 | 37 | 3450×2500×2350 | |
25×3200 | 25 | 3200 | 3505 | 900 | 5 | 20-1000 | 3°7′ | 150 | 37 | 4160×2600×2500 | |
30×2500 | 30 | 2500 | 2825 | 900 | 4 | 20-1000 | 3°12′ | 200 | 45 | 3500×2650×2500 | |
30×3200 | 30 | 3200 | 3450 | 1000 | 4 | 20-1000 | 3°12′ | 200 | 45 | 4350×3050×2800 |
Details of Hydraulic Swing Shearing Machine
Hydraulic valve block:Brand hydraulic valve group, derived from Bosch Rexroth, Germany. Strong power, stable performance. The noise is small.
Schneider, electrics inverter: High quality electric pears can perform well even the eclectricity is not stable and customers can easily get the replacement anywhere in the world. The motors for backgauge stroke are controller by inverter, which can achieve high positioning accuracy of the backbauge.
Working bench feeding balls: Feeding balls of workbench can reduce friction, protect the workpiece surface. Safety fence: left, right and front protective guard to ensure operator safety.
Front supporter arms: Make it easy to handle the work and feeds the material throught the cutting area by providing more delicate and quicker cuttings. Length is customized, measured by mm strong front support arms with slot and stopper.




Quality motor: Brand motor improves the lifespan of the machineand keeps the machine working in low noise enviroment. Siemens motor is options. Sunny pump: World famous brand Sunny for hydraulic pump performs well and provides great power for the world hydraulic system.
Ball screw timing belt transmission: High-precision back gauge device, fine ball screw and polished rod structure, high performance motor drive. Unique timing belt transmission mechanism,reliable and stable.
Pneumatic backge: Avoids hanging down the wide and thin sheets via pneumatic table support and provides more precise cuts.



Light curtains for finger protection: LNTECH light curtain designed to enable easy and quick material handling with high-protection.
Laser alignment lamp: Provides qualified and sensitive cutting by casting a line shadow at the cutting edge for right positioning of the worksheet to be cut.


Applications of Hydraulic Swing Shearing Machine
- Sheet metal processing: used for straight line cutting, arc cutting and curve cutting of metal sheets.
- Metal structure manufacturing: In the construction, shipbuilding, automobile and other industries, it is used for cutting, straightening, trimming and other operations of metal sheets.
- Punching processing: Complete the punching function of the plate for assembly of parts or ventilation and drainage.
- Customized processing services: Provide adjustable cutting length and angle to meet customers’ personalized processing needs.
- Aviation, light industry, metallurgy, chemical industry: provide special machinery and complete sets of equipment required for these industries.