Introduction
In the field of modern metal processing, CNC press brake machine has become the key equipment to realize accurate forming of sheet metal. With the increasing demand for high precision, high efficiency and high flexibility in manufacturing industry, it is very important to deeply understand its working principle. This paper will comprehensively analyze the mystery of CNC press brake machine from mechanical structure to numerical control system.
I. Overview of CNC press brake machine
1.1 Important position in the field of metal processing
In the metalworking industry, CNC press brake machine is widely used. In automobile manufacturing, metal plates used for body and parts are bent, such as the production of doors and hoods; In the aerospace field, it undertakes high-precision bending processing of aircraft structural parts; In light industry, realize efficient and accurate bending of metal shell of household appliances; Shipbuilding, elevator and railway vehicle manufacturing are also inseparable from it. Its key application in various industries highlights its core role in promoting product manufacturing upgrade, and it is an essential equipment for metal processing.
1.2 Comparative advantages with traditional bending machine
The traditional bending machine relies on the experience of operators and manual debugging, which is prone to human error and limited in machining accuracy. The CNC press brake machine is equipped with advanced numerical control system, which can accurately set the bending parameters.
1.3 Examples
In the processing of precision electronic equipment, the angle deviation can be controlled in a very small range. In terms of production efficiency, it is tedious and time-consuming to manually calibrate the mold and debug parameters when the traditional machine changes tasks. CNC press brake machine has powerful storage function, can switch programs with one button, and automatically locate the mold, which is 30%-50% higher than the traditional machine. In the face of complex shapes, traditional machines are limited by manual precision and simple molds. CNC press brake machine can easily deal with it with multi-axis linkage technology, such as the processing of aerospace complex wing connectors.
II. The mechanical structure of CNC press brake machine
2.1 Analysis of Core Mechanical Components
2.1.1 Synchronization system
The synchronization system consists of torsion shaft, lower rocker arm and joint bearing. The torsion shaft transmits power to ensure the synchronization of both ends of bending, and the lower rocker arm and joint bearing maintain stable and accurate mechanical action, which lays the foundation for high-precision machining and avoids inconsistent bending angles of plates.
2.1.2 Guide rail slider
The guide rail slider assembly comprises a guide rail slider, a hydraulic cylinder and a mechanical stop adjusting structure. The hydraulic drive cylinder pushes the piston rod to drive the slider to move, so that the bending pressure is stable and uniform, the operation flexibility and response speed are improved, and the processing requirements of different plates are met.
2.1.3 Stop mechanism
The stop mechanism is driven by motor and the ball screw is driven by chain, and its position and size are controlled by CNC system. Accurate positioning of materials before bending to ensure processing accuracy and consistency is the quality guarantee of batch and customized processing.
2.2 Influence of mechanical structure on machining accuracy
The mechanical structure of CNC press brake machine is closely related to machining accuracy. The accurate synchronization of the synchronization system, the stable pressure of the guide rail slider and the accurate positioning of the stop mechanism reduce the deformation error of the plate and ensure high-precision repetitive processing.
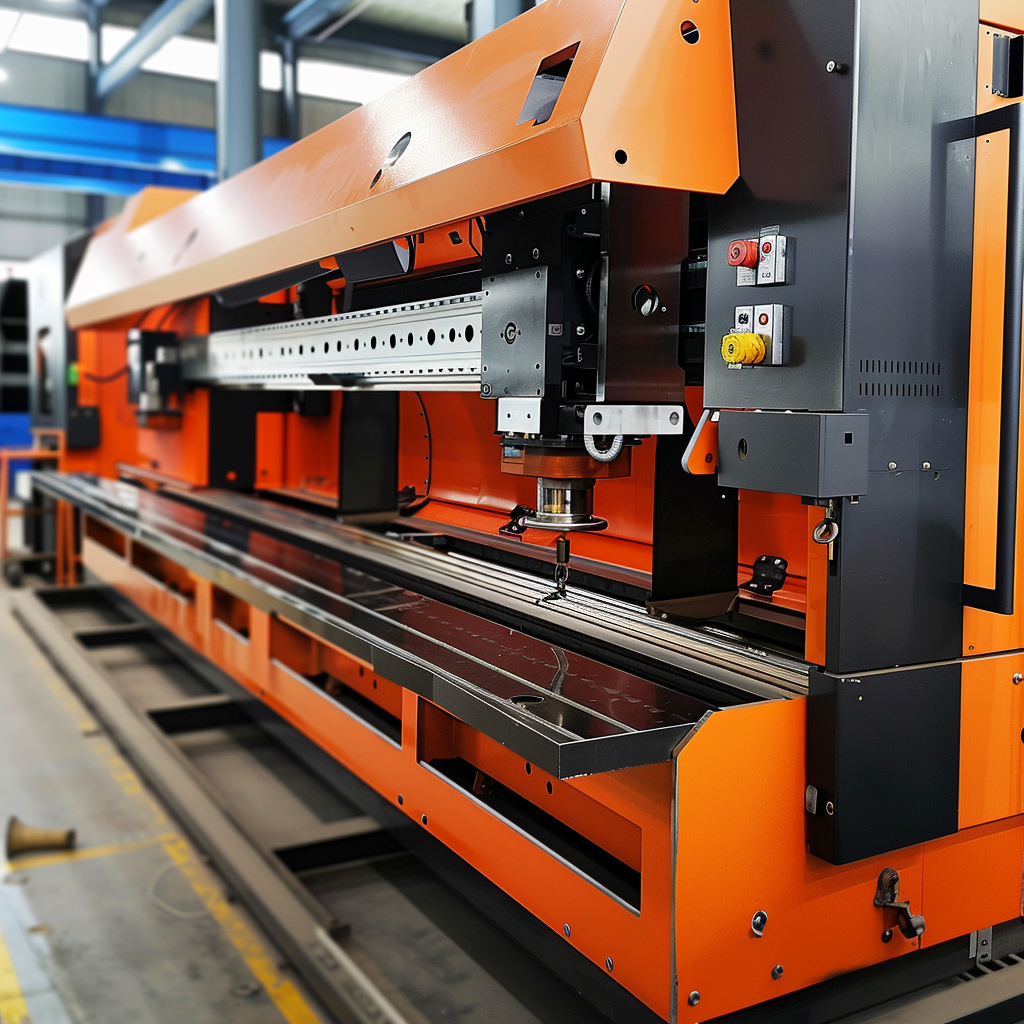
III. Electromagnetic clamping and forming principle of CNC press brake machine
3.1 Working Mechanism of Electromagnetic Clamping
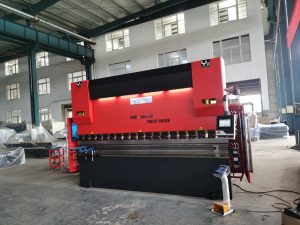
CNC press brake machine mainly relies on electromagnetic force to clamp metal plates. Dure processing, that electromagnetic device generate a strong magnetic force to fix the plate, which is more flexible than the traditional mechanical clamping, adapts to different plates, and the clam force can be accurately adjusted, thus creating conditions for processing complex shapes and ensuring stable processing without displacement errors.
3.2 Force and Motion Control in Forming Process
In sheet metal forming, firstly, electromagnetic clamping is carried out, and then the slide block of guide rail is driven by hydraulic pressure to bend according to the procedure. The CNC system monitors and adjusts the motion parameters of the parts in real time, such as the speed and pressure of the slider, to ensure uniform force and accurate angle. Such as automobile body parts manufacturing, to ensure that the bending shape conforms to the design and ensure the quality and performance.
IV. The key role of CNC system in CNC press brake machine
4.1 Function Overview of CNC System
Numerical control system is the “brain” of CNC press brake machine, which accurately controls the movement of mechanical parts, locates the bending parameters of sheet metal, has powerful programming function, can write programs according to requirements, can also monitor the running state, collect and analyze data, and ensure the smooth processing.
4.2 Convenience of programming and operation
Numerical control system supports various programming modes, such as DA53T and DA66T control systems. Operators can generate programs by inputting sheet information, and the operation interface is friendly, and novices can easily get started, which is convenient for switching tasks and improving production efficiency.
4.3 CNC system and mechanical structure work together
The CNC system instructs the mechanical parts and structures to perform actions according to the program, and the system monitors the feedback and optimizes the instructions during the process. For example, automatically adjust hydraulic parameters when detecting slider deviation to ensure machining accuracy and stability.
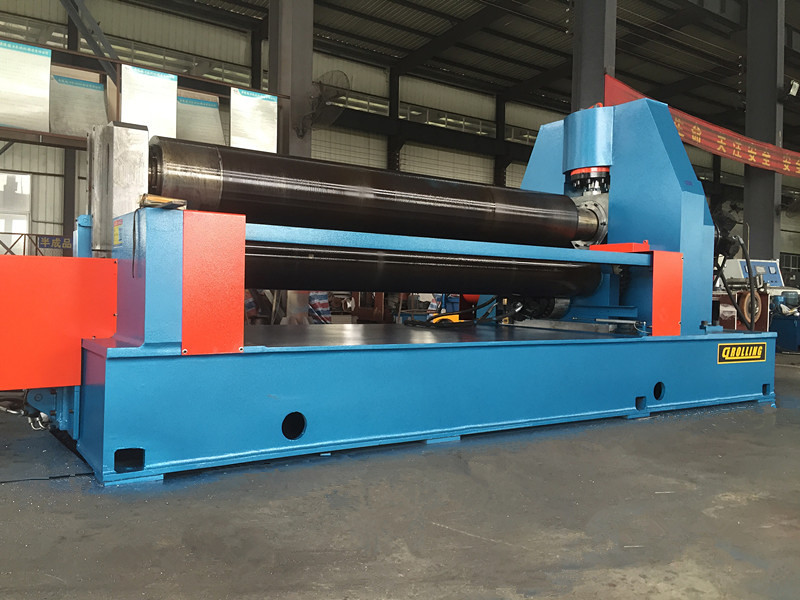
V. Development Trend of Automation and Intelligentization of CNC press brake machine
5.1 Realization of Automatic Production
With the intelligent upgrading of manufacturing industry, the automation degree of CNC press brake machine is improved, and it can be connected with robot arm and material conveying system to realize full automation of sheet metal processing. Robots feed and discharge materials, reducing the influence of human factors and improving production efficiency and product consistency.
5.2 Application and advantages of intelligent function
Its intelligent function is rich, the sensor senses the characteristics of sheet metal, automatically adjusts parameters, intelligently diagnoses and predicts faults, and the production management system analyzes data to assist decision-making, reducing costs, promoting product innovation and enhancing the competitiveness of enterprises.
5.3 The influence on the future metal processing industry
The development of CNC press brake machine promotes the metalworking industry to move towards high precision, high efficiency and low cost, reduces manual dependence, improves safety, leads the trend of intelligent manufacturing, and promotes product diversification and high-quality development.
VI. Features of CNC Hydraulic Press Brake Bending Machine WE67K
6.1 Performance Highlights of WE67K
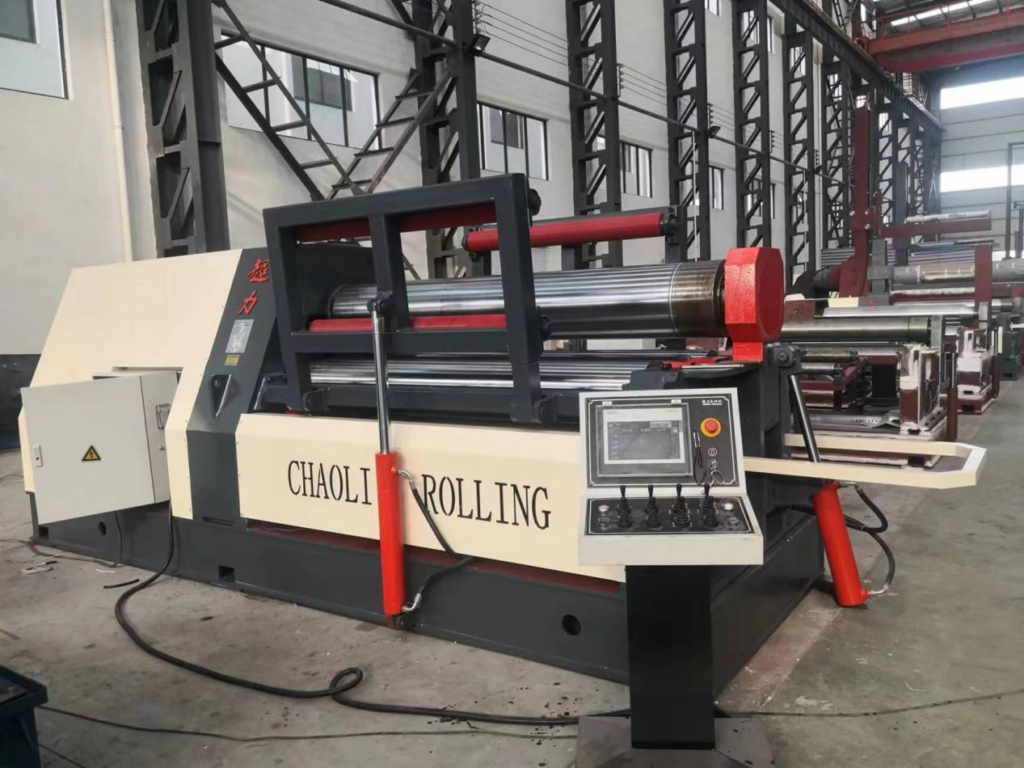
CNC Hydraulic Press Brake Bending Machine WE67K has excellent performance and strong bending ability, and is suitable for various plates. High-precision synchronization and hydraulic system ensure accurate and stable processing, such as excellent performance in processing stainless steel plates. The numerical control system has diverse programming, simple operation and improved efficiency.
6.2 Differences and advantages with other models
Compared with other models, the mechanical structure of WE67K is optimized, and the precision of guide rail slider and stop mechanism is improved. The numerical control system has stronger data processing and intelligent functions, and can realize complex processes. High reliability, using high-quality components and advanced technology, reducing maintenance costs.
VII. How to choose the right CNC press brake machine?
7.1 Selection according to production requirements
Enterprises should consider the production demand when choosing CNC press brake machine. Large-scale production industry selects equipment with strong processing and high efficiency; High-precision parts manufacturers focus on precision. At the same time, pay attention to the thickness range of plate material and adapt to processing equipment.
7.2 Consider the level of accuracy and automation
Accuracy and automation level are key indicators. High-precision equipment ensures quality, automation equipment improves efficiency and reduces labor costs. Enterprises weigh the demand according to the scale budget and choose the equipment with high cost performance.
7.3 Evaluating manufacturers and after-sales service
It is very important to choose reliable manufacturers and high-quality after-sales service. The product quality and after-sales of well-known brands are guaranteed, and the excellent technical innovation and customized service can meet the individual needs.
VIII. Maintenance and maintenance points of CNC press brake machine
8.1 Key links of daily maintenance
Daily maintenance is the basis of normal operation of equipment. Operators need to clean the equipment, check the lubrication and electrical system, maintain the mold, keep the equipment clean and tidy, reduce the wear of parts, prevent electrical anomalies, and ensure the bending quality.
8.2 Importance and content of regular maintenance
Regular maintenance is the key to prolong the service life and performance of equipment. Including comprehensive inspection and maintenance of mechanical parts, oil change and cleaning of hydraulic system, software upgrade and backup of numerical control system, etc., which are operated by professionals to solve potential problems in time.
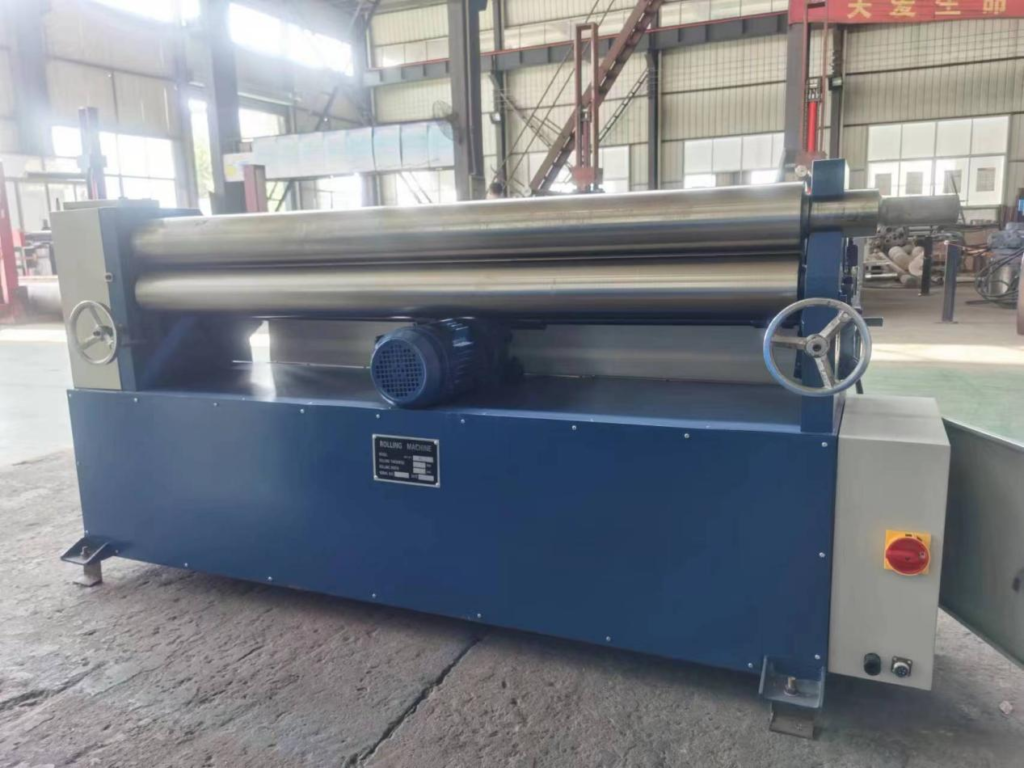
8.3 Influence of maintenance on equipment life and performance
Good maintenance can prolong the service life of equipment and maintain high performance. Reduce the failure probability and maintenance cost, ensure the mechanical accuracy and stability, and improve the processing quality. For example, the maintenance of guide rail slider can improve the bending accuracy.
IX. Conclusion
CNC press brake machine works together from mechanical structure to numerical control system to realize high-precision sheet metal bending. It is widely used in many industries to promote development, and the trend of automation and intelligence brings innovation breakthroughs. Enterprises should consider demand and pay attention to maintenance when selecting equipment, which will continue to play a key role in the field of metal processing in the future and lead the industry towards intelligence and efficiency.