Machine Introduction
The Press Brake Bending Machine WC67Y is a common and widely used metal processing equipment, mainly used for precise bending of metal sheets. Its working principle is based on the principle of mechanical lever and torque transmission, combined with simple and reliable structural design and convenient operation, making it widely used in the field of metal processing.
This equipment usually consists of a base, a torsion axis system, an upper mold and a lower mold. The operator first places the metal sheet to be processed on the workbench and positions and adjusts it as needed. Then, the torsion shaft system is driven through a handle or pedal to cause the torsion shaft to start rotating. The rotation of the torsion shaft is converted into linear motion through a gear and lever system, pushing the upper mold downward.


When the upper mold comes into contact with the metal sheet, pressure is applied to cause the metal sheet to plastically deform between the upper mold and the lower mold, thereby forming the required bending angle. During the entire bending process, the operator can control the descending depth of the upper mold by adjusting the position of the torsion axis, thereby achieving precise control of the bending angle.
The press broke bending machine has the advantages of simple structure, convenient operation and low maintenance cost. Its working principle is stable and reliable, and can meet the bending processing needs of various metal sheets. Therefore, it has been widely used in metal processing, manufacturing, automotive industry, aviation industry and other fields.
Features
All steel welded structure: The press brake bending machine adopts an all-steel welded structure and has the function of vibration and stress relief, thus ensuring the high strength and good rigidity of the machine. This structural design enables the machine to maintain a stable working condition even during long-term operation, ensuring processing quality and efficiency.
Advanced E21 control system: This model is equipped with the advanced E21 control system, which can accurately control the movement of the slider and backgauge to achieve high-efficiency and high-precision positioning. At the same time, the upper mold is also equipped with a deflection compensation mechanism, which can effectively solve the deformation problem during processing and ensure processing accuracy.
The upper mold is equipped with a deflection compensation mechanism: This model also has an economical upper mold clamp, which is fine-tuned through inclined iron, making it simple and practical. The mold can be specially customized according to the requirements of the bent workpiece to meet different processing needs and improve the flexibility and applicability of the machine.
Integrated hydraulic system: The press brake bending machine uses an integrated hydraulic system and hydraulic components and seals from world-renowned companies to reduce hydraulic pipelines to a minimum, thereby ensuring a high degree of reliability and safety in machine operation. At the same time, the E21 controller and foot switch are equipped with emergency stop buttons to protect the operator’s personal safety.
High-precision backgauge system: This model is also equipped with the function of smooth movement of the rear gauge, making the operation more convenient and faster, and improving work efficiency.
Technical Parameters
- Models: 40T/1600, 40T/2000, 40T/2500, 63T/2500, etc., covering the needs of different tonnages and workbench lengths.
- Nominal pressure: Depending on the model, the work pressure also varies.
- Worktablelength: From 1600mm to 6000mm, it is suitable for plate processing of different sizes.
- Distance between column: 1280mm to 4700mm, providing enough bending space.
- Throat depth: From 250mm to 500mm, adapt to bending needs of different depths.\
- Opening height: From 325mm to 600mm, openings of different heights facilitate the bending and picking up of large workpieces.
- Motor power: From 4kw to 45kw, varies according to different models and working requirements.
- Machine size: Depending on the different models, the size also varies, such as1850×1300×2100mm, 2250×1300×2100mm, 2750×1300×2100mm and so on.
Model | Nominal pressure | Worktable length | Distance between column | Throat Depth | Stroke | Opening | Motor | Dimension |
Ton | mm | mm | mm | mm | mm | kw | mm | |
40T/1600 | 40 | 1600 | 1280 | 250 | 120 | 325 | 4 | 1850×1300×2100 |
40T/2000 | 40 | 2000 | 1550 | 250 | 120 | 325 | 4 | 2250×1300×2100 |
40T/2500 | 40 | 2500 | 2050 | 250 | 120 | 325 | 4 | 2750×1300×2100 |
63T/2500 | 63 | 2500 | 2050 | 250 | 120 | 360 | 5.5 | 2750×1350×2230 |
63T/3200 | 63 | 3200 | 2600 | 250 | 120 | 360 | 5.5 | 3450×1350×2230 |
80T/2500 | 80 | 2500 | 2050 | 320 | 120 | 380 | 7.5 | 2750×1400×2350 |
80T/3200 | 80 | 3200 | 2600 | 320 | 120 | 380 | 7.5 | 3450×1400×2350 |
100T/2500 | 100 | 2500 | 2050 | 320 | 120 | 380 | 7.5 | 2750×1450×2380 |
100T/3200 | 100 | 3200 | 2600 | 320 | 120 | 380 | 7.5 | 3450×1450×2380 |
100T/4000 | 100 | 4000 | 3200 | 320 | 120 | 380 | 7.5 | 4250×1450×2380 |
125T/2500 | 125 | 2500 | 2050 | 320 | 120 | 380 | 7.5 | 2750×1450×2380 |
125T/3200 | 125 | 3200 | 2600 | 320 | 120 | 380 | 7.5 | 3750×1450×2380 |
125T/4000 | 125 | 4000 | 3200 | 320 | 120 | 380 | 7.5 | 4250×1450×2380 |
160T/3200 | 160 | 3200 | 2600 | 320 | 180 | 450 | 11 | 3450×1700×2600 |
160T/4000 | 160 | 4000 | 3200 | 320 | 180 | 450 | 11 | 4250×1700×2600 |
200T/3200 | 200 | 3200 | 2600 | 320 | 200 | 470 | 15 | 3450×1850×2860 |
200T/4000 | 200 | 4000 | 3200 | 320 | 200 | 470 | 15 | 4250×1870×2950 |
250T/3200 | 250 | 3200 | 2600 | 400 | 250 | 530 | 18.5 | 3450×1920×3050 |
250T/4000 | 250 | 4000 | 3200 | 400 | 250 | 530 | 18.5 | 4250×1950×3150 |
300T/3200 | 300 | 3200 | 2600 | 400 | 250 | 560 | 22 | 3450×2200×3130 |
300T/4000 | 300 | 4000 | 3200 | 400 | 250 | 560 | 22 | 4250×2250×3320 |
300T/6000 | 300 | 6000 | 4700 | 400 | 250 | 560 | 22 | 6100×2250×4250 |
400T/3200 | 400 | 3200 | 3200 | 400 | 300 | 640 | 30 | 3200×2280×3250 |
400T/4000 | 400 | 4000 | 3200 | 400 | 300 | 640 | 30 | 4000×2300×3600 |
400T/6000 | 400 | 6000 | 4700 | 400 | 300 | 640 | 30 | 6000×2350×4650 |
500T/4000 | 500 | 4000 | 3200 | 500 | 310 | 640 | 37 | 4000×2480×4330 |
500T/6000 | 500 | 6000 | 4700 | 400 | 310 | 640 | 37 | 6000×2450×4700 |
600T/6000 | 600 | 6000 | 4700 | 460 | 310 | 650 | 45 | 6000×2700×5710 |
Details
Famous motor brands, Schneider control electrical components.
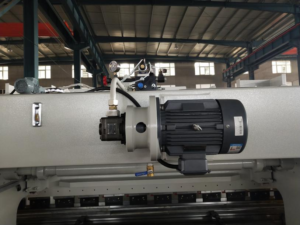
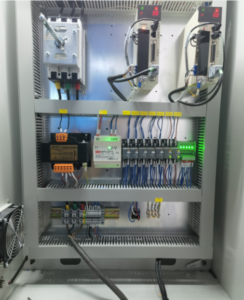
Famous servo motor brands, configure with Sunny pump.

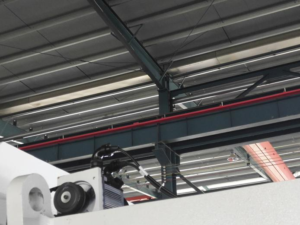
Servo driver, German JS card sleeve joint.
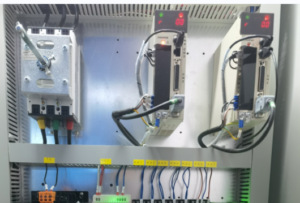
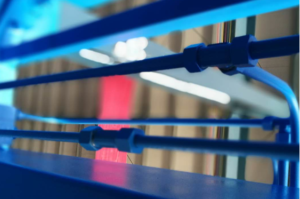
High precision and stability rear material blocking system, mechanical fixture for mold installation, safer when changing molds. The mechanical clamp on the upper mold makes it safer when changing molds.

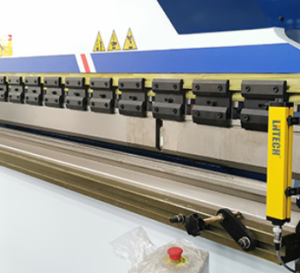
Portable foot switch. Configure with safety guardrails.
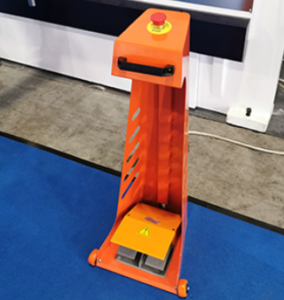
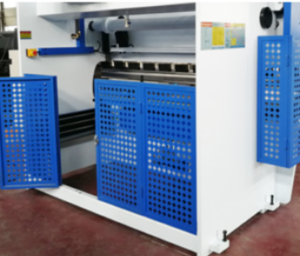
Larger closure height, throat depth, inner gear distance, and slider stroke facilitate the bending and retrieval of large and complex workpieces.
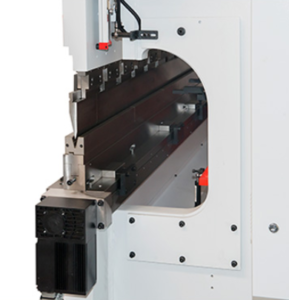
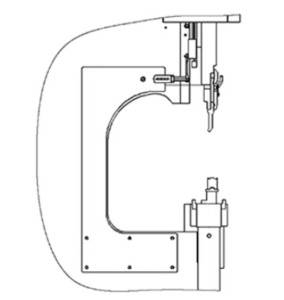
ESTUN E21NC control system. Mechanical deflection compensation device.
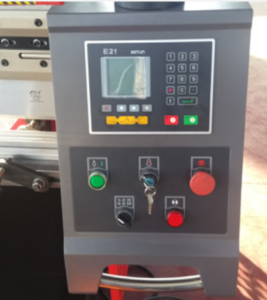
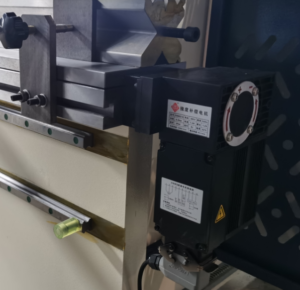
Mechanical deflection compensation device:
1. Adopting a bidirectional wedge block adjustment structure, it can meet the compensation adjustment of the machine tool in both horizontal and vertical directions.
2. This structure adopts a dense point compensation method to make the bending accuracy more accurate.
3. Compensation for bending materials with the same plate thickness is in place, which is different from the structure of hydraulic compensation that continuously moves back and forth. Mechanical compensation greatly reduces fatigue deformation of the airport workbench and improves its service life.
4. Using dedicated reducers and high-precision potentiometers for precise control of compensation accuracy values.
5. Unlike the three plate structure of hydraulic compensation worktable, this device adopts a single plate worktable design, which can effectively prevent interference in bending workpieces.
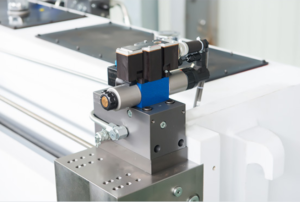
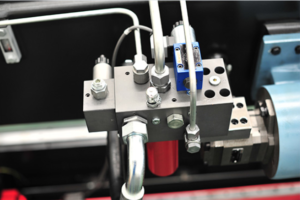
Hydraulic system, adopting integrated hydraulic control system, simplifying pipelines, and adopting efficient bite type anti leakage joints
To prevent leakage. Improve the stability of machine tool operation, while also making the appearance more concise and beautiful. Sunny imported pumps and Rexroth valve groups ensure low overall system noise and long service life.
Optional accessories
1. The safety light curtain provides safety protection. If a foreign object enters the work area during operation, immediately release a hold and the machine tool will stop working.

2. Quick mold change. Photoelectric protection device.
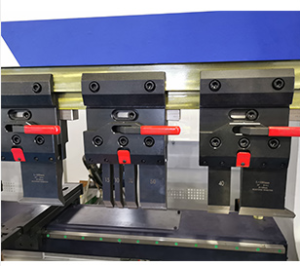

3. Manual compensation workbench, generally recommended for use at least 4 meters, can effectively improve product straightness. Movable support arm.
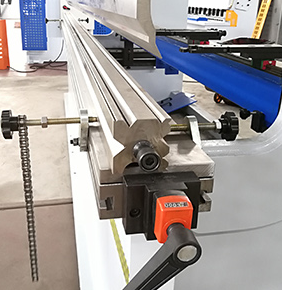
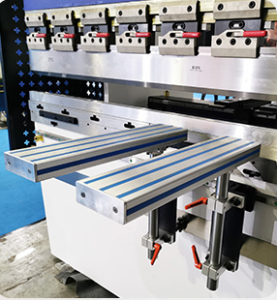
4. Various operating systems.
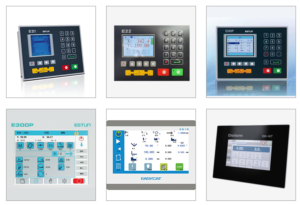
TP10S system function introduction
1. Control with Axis X+Y axis
2. 4 inch touch screen
3. Support with mechanical/hydraulic compensation
4. Internal machine tool movement logic,Multiple action mode
5. Internal mold base, material sheet can be edited
6. I/O Ports are freely configurable
7. With USB interface,Easy backup upgrade
8. With parameter backup/ restore function
9. With English/Chinese language
10. Metric/British system
11. Angle programming
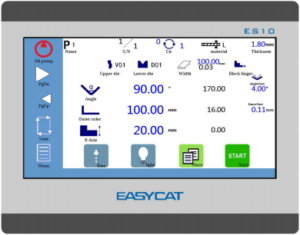
Applications
- Metal processing: For straight, arc and curved cutting of sheet metal.
- Aerospace: It used in precision bending processing in the manufacturing of aircraft structural parts.
- Automobile industry: It used for bending metal parts such as automobile bodies and chassis.
- Construction navale : It used for bending processing of hull structures and internal metal decoration.
- Electrical industry: It used for processing metal shells such as electrical cabinets and switch cabinets.
- Industrie de la construction : It used in the production of metal roofs, fences and other building components.


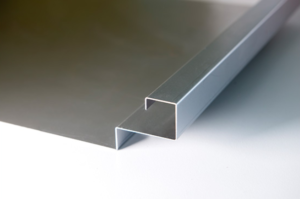