The origin of automobile manufacturing reform
In the vast field of automobile industry, which is full of innovation and precision demand, the profile bending machine is like a rising star and has become a key force to promote the progress of the industry. Its origin can be traced back to the basic demand for precise metal shaping, and now it has evolved into an indispensable cornerstone in the development of automobile engineering.
The automobile industry has always been in the wave of technological innovation, constantly pursuing the improvement of vehicle performance, safety and aesthetics. Metal profile bending technology plays an important role in this long journey. This change is undoubtedly a revolutionary leap from the simple manual bending process in the past to the highly precise and automatic system at present.
The types of profile bending machine
Multifunctional bending machine
Bending machine can be called the mainstay in the field of automobile parts manufacturing. This kind of machine has the magical ability to shape metal profiles into smooth and continuous curves with a set of carefully designed rollers. When manufacturing components such as chassis longitudinal beam and exhaust pipe, the bending machine is the best choice. The secret lies in the adjustable roller, which can accurately set the required bending radius. Taking the exhaust pipe manufacturing of a fashionable sports car as an example, the bending machine endows it with elegant radian, which not only improves the aesthetic appearance, but also optimizes the exhaust airflow, thus enhancing the engine performance.

Accurate bending machine
When the manufacturing task involves sharp angles and complex and fine shapes, the press-bending machine will debut. With the help of powerful hydraulic or mechanical pressure device, it can exert precisely controlled force on specific points of metal profiles to achieve precise bending. This makes it occupy an important position in the manufacture of parts such as body frame bracket and door hinge. Imagine the precise angle required for the door frame of a luxury car. The press bending machine ensures that every bending is accurate, thus ensuring perfect assembly and smooth opening and closing.
Powerful hydraulic profile bending machine
Hydraulic profile bending machine is like a giant with infinite strength in the field of automobile manufacturing. With the powerful power of the hydraulic system, it can easily deal with the thickest and strongest metal profiles. In the construction process of heavy truck chassis, hydraulic profile bending machine plays an important role in the face of high-strength steel beams. It provides sufficient strength and fine control to ensure that the quality of these heavy materials is not damaged when bending, so that the chassis can withstand the severe test of heavy load and long journey.
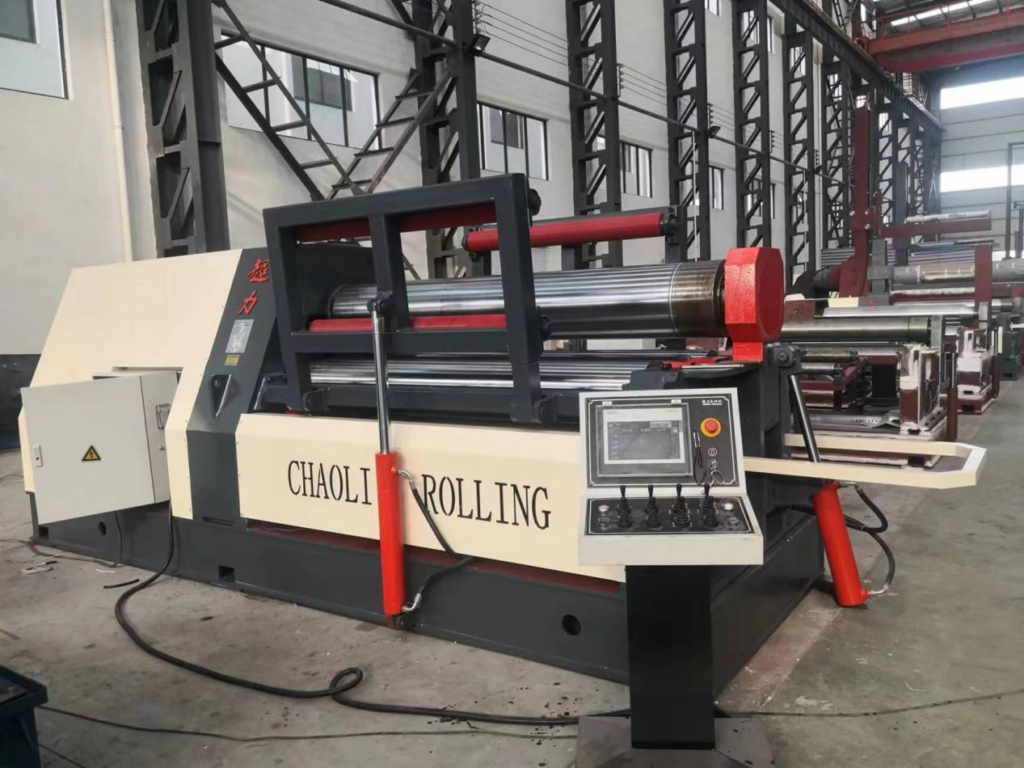
The subtle mystery of the working mechanism
Artistic Cooperation between Mould and Roller
In the world of roll bending machine, the roller is like a shape-shaping artist. Its diameter, surface texture and spacing have been carefully adjusted to perform a perfect bending movement. Similarly, in the press bending machine, the die is tailored according to the unique geometric shape of each profile, and the bending task is performed as accurately as a scalpel. The interaction between metal profiles and these molds or rollers is just like an exquisite ballet dance, and every movement and adjustment show the perfect integration of engineering art and science. For example, rollers coated with cemented carbide are often used to resist the wear force and keep in good condition throughout numerous bending operations.

Surging power of hydraulic system
The hydraulic system in the profile bending machine is like a powerful heart, which injects continuous energy and precise control into the bending process. Hydraulic cylinder drives the movement of roller or pressure device by virtue of its ability to generate great power, and realizes smooth and adjustable bending operation. The pressure and flow of hydraulic oil can be fine-tuned with amazing accuracy, which enables manufacturers to customize the bending process according to the characteristics of materials and profiles. In the face of the stringent quality standards of the automobile industry, this level of control is by no means dispensable, but an absolute necessity.
Close ties with auto parts manufacturing
Chassis: the backbone of automobile engineering
Chassis is undoubtedly the core skeleton of a car, and the profile bending machine is a skillful craftsman who carves its shape. The bending machine is responsible for shaping the chassis longitudinal beam and cross beam, ensuring their precise alignment and providing the structural integrity needed to support the whole vehicle. Hydraulic profile bending machine tames thick steel plates used for heavy chassis construction by virtue of its powerful power control ability. Even a slight bending deviation on chassis components may lead to serious consequences, such as impaired handling, reduced durability and even endangering driving safety.
Exhaust system: the breathing passage of the vehicle.
In the production field of exhaust system, the profile bending machine is like a magical magician, creating complex and changeable bends and shapes. The roll bending machine gives the exhaust pipe a continuous and smooth curve, optimizes the airflow and reduces the back pressure, thus improving the engine efficiency. The press bending machine builds the mounting bracket and flange with meticulous accuracy to ensure tight connection and no leakage. The role of profile bending machine in exhaust system manufacturing is not only related to performance, but also a key boost to achieve environmental protection and compliance, which is reflected by accurately shaping the catalytic converter shell and other emission control components.
Body frame and structure: beautiful and protective shell
The car body frame and structure are the harmonious unity of beauty and function, and the profile bending machine is the conductor of this harmonious movement. The bending machine is responsible for shaping the curved roof rack and body panel, adding elegance and strengthening structural rigidity. The press bending machine carefully builds the door frame, pillars and other fine parts, achieving the accuracy of a millimeter. The seamless connection between these parts realized by the profile bending machine is not only a powerful proof of engineering Excellence, but also an important guarantee for vehicle safety and appearance.
Catalysts for Automobile Design and Innovation
Breaking through the boundaries of geometric shapes
Mesin pembengkok profil opens a door to infinite possibilities for automobile design. With unparalleled precision and flexibility, automotive engineers can now conceive the geometry of parts that once existed only in science fiction imagination. For example, the curved and sculptural body panel not only makes the vehicle become the focus of attention on the road, but also significantly improves its aerodynamic performance and reduces wind resistance, thereby reducing fuel consumption and improving driving stability. This innovative design language makes the car not only meet the functional requirements, but also become a flowing work of art, showing its unique brand personality and charm.
Promoters of Lightweight and Material Optimization
Under the general trend of pursuing fuel efficiency and emission reduction in automobile industry, lightweight has become a key strategy, and profile bending machine plays an important role in it. It enables thinner and stronger materials to be applied, and through accurate bending process, the overall weight of the vehicle is reduced while ensuring the structural strength requirements. Taking the application of aluminum alloy in body frame and chassis components as an example, advanced profile bending technology overcomes many challenges of aluminum alloy material bending, and realizes efficient utilization and performance optimization of materials. This not only helps to improve the fuel economy of the vehicle, but also brings significant improvement in handling and acceleration performance, bringing drivers a more agile and agile driving experience.
Challenges and Countermeasures in the Application of Automobile Industry
Material compatibility and handling problems
A variety of materials are widely used in the automobile industry, covering different grades of steel, aluminum and composite materials. It is a challenging task to ensure that the profile bending machine is compatible with these materials and can handle them effectively. Compared with steel, the mechanical properties of aluminum are significantly different, which requires specific molds, processing parameters and process settings. Manufacturers must invest a lot of resources in research and development to optimize the profile bending machine for different material combinations and thicknesses. For example, specially designed rollers, molds and accurately adjusted hydraulic systems are used to prevent material damage and achieve accurate bending. In addition, the proper handling and storage of materials are equally important to maintain their quality and integrity before and after bending.
The rigorous test of precision and tolerance control
The requirements for precision and tolerance of automobile parts are almost harsh. Even the smallest dimensional deviation may have a serious impact on the performance and safety of vehicles. The profile bending machine must be equipped with advanced measurement and control system to ensure that the bent profile meets these high standards. Laser measurement and feedback system plays an increasingly important role in real-time monitoring of bending process, which can find deviations in time and adjust them immediately. At the same time, manufacturers need to establish strict quality control procedures to verify the accuracy of curved profiles in all aspects of production. This includes accurate size detection, material performance testing and comprehensive process audit to ensure the consistency and reliability of product quality.
Exploration Road of Automation and Production Line Integration
In order to meet the demand of mass production and compact production plan in automobile industry, profile bending machine needs to be integrated into automatic production line. This requires seamless information interaction and cooperation with other manufacturing links such as welding, machining and assembly. With the vigorous development of Industry 4.0 technology, the application of Internet of Things (IoT) and artificial intelligence (AI) provides strong support for this goal. Intelligent profile bending machine can automatically receive production orders and automatically adjust equipment parameters according to the requirements of the orders, optimize the production process and reduce human errors. In addition, the reasonable layout planning of the production line and the efficient automatic material handling system are also the key factors to ensure the perfect integration of the profile bending machine and the production line, so as to realize the efficient and smooth operation of the production process.
Future Prospect of Profile Bending Machine in Automobile Engineering
Deep integration of automation and robotics
Looking forward to the future, the profile bending machine will usher in the deep integration of automation and robot technology in the field of automobile engineering. The automatic feeding and blanking system will further improve the production efficiency, greatly shorten the production cycle and reduce the labor cost. The mechanical arm is expected to participate in the handling and positioning of metal profiles, ensuring higher accuracy and consistency, and significantly reducing the risk of human error. In addition, the machine learning algorithm will be integrated into the profile bending machine, so that it can learn and optimize the bending process independently based on historical data and real-time feedback. This will push the production accuracy and efficiency to a new height, for example, the machine can automatically learn and master the best bending parameters of different materials and profiles, thus greatly reducing the equipment debugging time and material waste.
Innovative integration of additive manufacturing and profile bending
The integration of additive manufacturing (3D printing) and profile bending is a new trend with great potential in automobile industry. Additive manufacturing can create complex and unique geometric shapes and customized parts, and profile bending can further strengthen and optimize these parts. For example, the bracket manufactured by 3D printing can obtain the required precise angle and shape after the profile is bent, providing innovative solutions for specific automotive applications. This mixed manufacturing mode will enable automobile manufacturers to produce highly customized parts with excellent performance, break through the boundary between traditional design and engineering, and open up a broad space for the personalized and high-performance development of automobiles.
The rise of sustainable and environmentally friendly technologies
With the increasing emphasis on sustainable development in the automobile industry, environmental protection profile bending technology will become the core focus of future development. This covers many aspects of innovation and improvement, such as adopting energy-saving and efficient hydraulic system to reduce energy consumption; Use recycled materials to make molds and tools to reduce resource waste; Optimize bending process to reduce waste. Manufacturers will also actively explore the use of renewable energy to provide power for the profile bending machine, further reducing its environmental impact. For example, using biodegradable hydraulic oil to replace traditional petroleum-based hydraulic oil, and establishing a recycling system of metal waste, practicing the concept of environmental protection in the whole life cycle from raw material procurement to product manufacturing, and contributing to the green transformation of the automobile industry.
Conclusion: Profile Bending Machine—the Mainstay of Automotive Engineering in the Future
In conclusion, the profile bending machine has defined its place within the realm of automobile engineering and has, therefore, defined the future of this sector from several aspects simultaneously. Whether it is the manufacturing process for highly complex precision parts or fostering design innovation and lightweight processes, or even exploring new technologies to tackle future challenges, profile bending machines are found to have irreplaceable value. Though there are still many problems to be solved in terms of material compatibility, precise control, and automation integration, the problems are already solved in the future, opening a more efficient and sustainable development path for it. Due to the change that continues to take place in the automobile industry, the profile bending machine will stay important in meeting the ever-increasing demand of people who want safer, more efficient, and more aesthetic automobiles.

Manufacturers who actively embrace and invest in this technology will seize the opportunity in the highly competitive automobile market and lead the industry to a new realm of excellent quality and innovative design. The continuous development and innovation of profile bending machine will not only inject continuous vitality into the automobile industry, but also have a far-reaching positive impact on the whole transportation and manufacturing industry, and become one of the important engines to promote global economic progress and growth.