Introduction
In the vigorous development of modern industry, profile bending machine is an indispensable key equipment in the field of metal processing, and its production quality is directly related to the foundation of many industries. From the shaping of steel profiles of large ships to the precise shaping of building steel structures, every operation of the profile bending machine carries strict requirements for accuracy and quality.

First, the selection of raw materials: the foundation of quality
The starting point of profile bending machine production lies in the selection of raw materials. High-quality steel is an essential element to build a tough “skeleton” of a bending machine. For profile bending machines, the selected steel should not only have high strength to withstand huge rolling pressure, but also have good toughness to prevent cracks from appearing under repeated stress.
Profile bending manufacturers are like meticulous treasure hunters in this process, and through strict component detection and mechanical performance tests, unqualified products are screened out from the source.
Only by ensuring the superior quality of raw materials can the subsequent complex processing procedures have a stable quality starting point, just like the foundation of a skyscraper, a slight difference may lead to a chain of hidden dangers of quality collapse.
Second, the precision processing technology: the ingenuity of carving details
Entering the processing stage, the manufacture of a profile bending machine is an ultimate pursuit of process details. The machining accuracy of shaft parts needs to be controlled at the micron level, which requires advanced CNC machining centers to make every mating surface smooth as a mirror with high-precision milling and grinding technology, so as to ensure low friction and high accuracy when the bending machine is running.
In the manufacturing of the profile rolling die, hot forging, quenching, tempering, and other heat treatment processes are indispensable, which endow the die with superior wear resistance and appropriate hardness, make it stable in the long-term extrusion process, ensure accurate radian for the profile, and meet the strict demands of different customers on the rolling accuracy of profile bending machine.
Third, strict testing process: strict quality control
Before the birth of the finished product, strict inspection is the highlight of the quality control of the bending machine. First of all, the dimensional accuracy detection, using the three-coordinate measuring instrument to scan the key dimensions of the profile bending machine in all directions, without letting go of any deviation, to ensure that its rolling specifications are in perfect harmony with the design blueprint.
Furthermore, the performance test, which simulates various working conditions, allows the profile bending machine to roll profiles with different thicknesses and materials and observes its running stability, the uniformity of rolling force output, and the response sensitivity of the electrical control system.
Only the profile bending machine that has passed this many tests can be qualified to be labeled as qualified and flow to the market and become the right-hand man on the industrial production line.
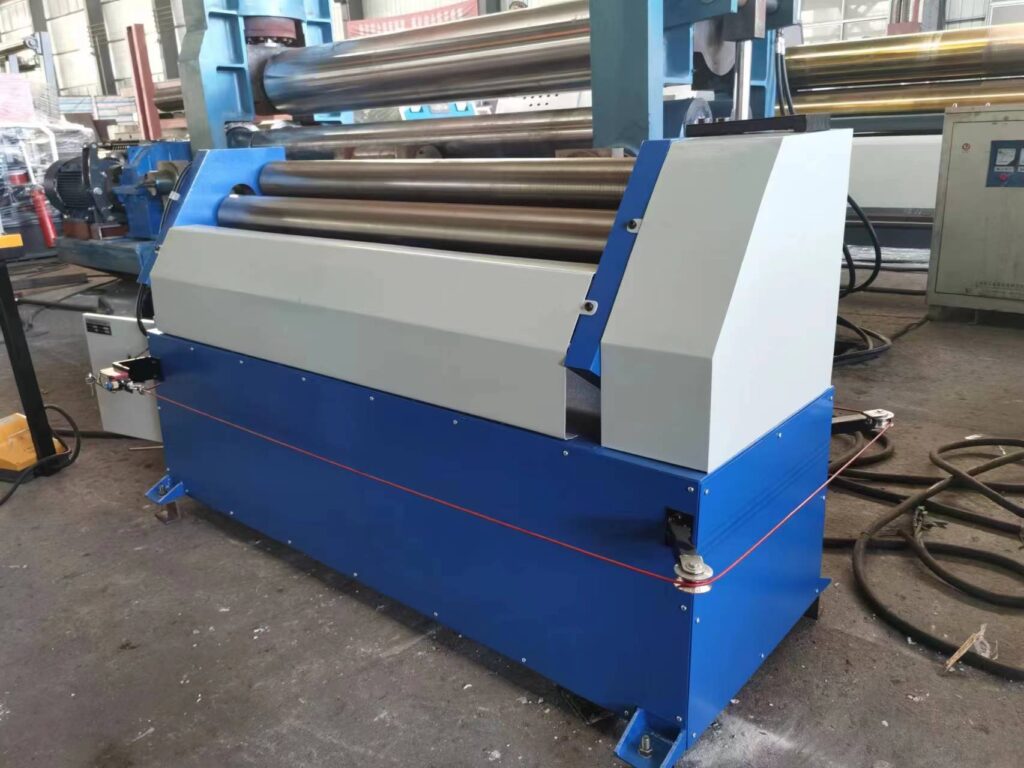
Conclusion
In today’s fierce competition, the quality control of profile bending machine production is a marathon without end. Whether it is the control of the source of raw materials, the meticulous processing, or the strict quality inspection before the finished product is released, every step embodies the wisdom and sweat of profile bending manufacturers.
Only by continuously strengthening the quality control system can the profile bending machine dance steadily on the industrial stage, contribute to the bright future of the global manufacturing industry, create an immortal legend in the field of metal processing with excellent quality, and make every profile bending operation a perfect display of precision and quality.