Welding technology is undoubtedly a key link in the modern shipbuilding process. With the development of science and technology, welding equipment has also undergone major changes. Among them, the application of conventional welding rotator has significantly improved the welding effect and efficiency, making the ship construction more efficient and precise. This article will deeply discuss the various applications of conventional welding rotator in shipbuilding, and the advantages and values it brings to the industry.
Basic functions
Conventional welding rotator are mainly used to support and rotate large workpieces, and their structures are usually composed of two or more rollers with driving devices. This equipment is especially suitable for welding cylindrical and conical metal parts. In shipbuilding, many large metal components are involved, such as hull, oil tank and deck, which often need to be accurately positioned and rotated during welding. By using the conventional welding rotator, the operator can easily adjust the position of the workpiece, realize 360-degree omni-directional welding, and effectively improve the welding accuracy.

Improve welding quality and efficiency
Welding quality and production efficiency are two core elements in shipbuilding. Traditional welding methods often require workers to constantly adjust the position of the workpiece, which not only increases the difficulty of manual operation, but also may lead to welding defects. By using conventional welding rotator, shipbuilding manufacturers can realize automatic welding and greatly reduce human errors. The data show that the welding time can be shortened by 30% to 50%, and the welding quality can be significantly improved, thus reducing the subsequent maintenance and repair costs.
Visualization and control of welding process
Conventional welding rotator design usually has a good operation interface and control system, which can monitor welding parameters in real time. Welders can clearly observe the progress of welding through the control panel and make adjustments in time. This controllable welding process provides a strong guarantee for welding quality.
Enhance welding flexibility
The conventional welding rotator also has good adaptability and can be adjusted according to the size and shape of different workpieces. Whether it is a small hatch cover or a large hull structure, it can be easily handled by using this equipment, showing great flexibility.
Promote safety and health
In the welding process of shipbuilding, safety is always the most important consideration. Factors such as high temperature, smoke and thermal radiation generated in welding operation may pose a threat to workers. Conventional welding rotator can raise the welding operation to a new safety level. By fixing the workpiece on the equipment, the welder can weld in a safer posture, reducing the workload and the risk of injury. In addition, the automation of the equipment also reduces the time for workers to work in potentially dangerous environments.
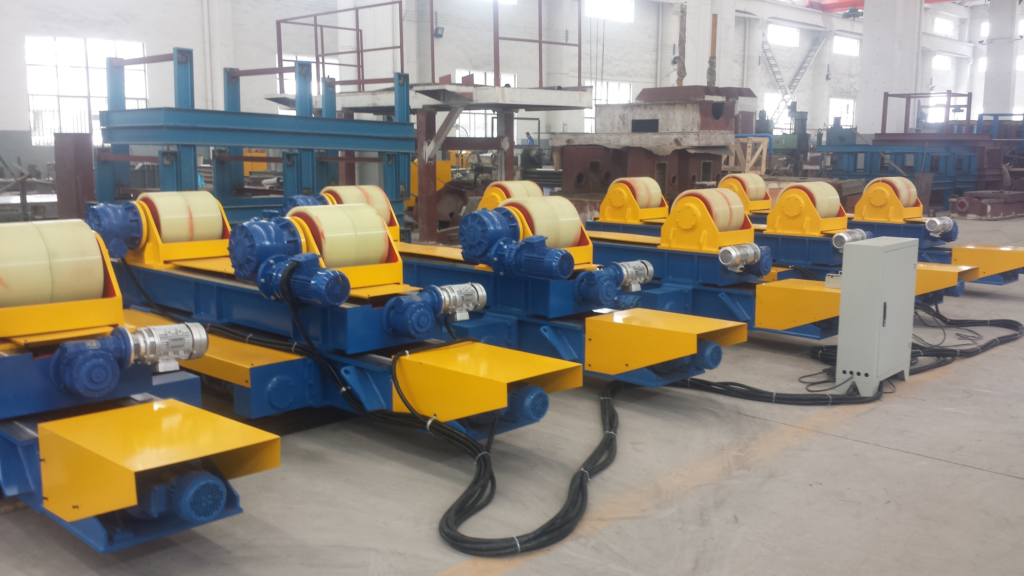
Conclusion
To sum up, the application of conventional welding rotator in shipbuilding not only improves the production efficiency and welding quality, but also enhances the safety, and has high flexibility and adaptability. With the continuous progress of shipbuilding technology, the importance of this equipment has become increasingly prominent, and it has played an irreplaceable role in improving the overall construction quality.
In the future, with the continuous improvement of precision and efficiency in shipbuilding, the technology of welding rotator will be upgraded and play a greater role. This tool is not only the booster of shipbuilding, but also the key to promote the innovation and development of the whole industry. In the fierce market environment, only with the help of advanced welding technology can ship manufacturers be in an invincible position in the competition. Therefore, investing in the advanced conventional welding rotator will bring tangible economic benefits and sustainable competitiveness to shipbuilding manufacturers.